پیشازاین سه مقاله در مورد نظریه محدودیت منتشر کردهایم. مقاله اول معرفی پنج گام تمرکزی، مقاله دوم فرآیندهای تفکر و حسابداری بهرهوری و مقاله سوم در مورد جنس محدودیتها و مثالی از استفاده عملی نظریه محدودیتها بود.
ما در این مقاله که چهارمین مقاله در مورد نظریه محدودیتها است، در تلاش هستیم نظریه محدودیتها را با روش تولید ناب ترکیب کنیم. ترکیب این دو تکنیک و استفاده از آن در واحدهای تولیدی میتواند تأثیر زیادی روی بازدهی مجموعههای تولیدی داشته باشد.
تضاد نظریه محدودیتها و روش تولید ناب
نظریه محدودیتها و تولید ناب (Lean Production) هر دو روشهای سیستماتیکی برای افزایش کارایی تولید هستند. این دو روش از رهیافتهایی کاملا متفاوت استفاده میکنند.
- نظریه محدودیتها روی شناسایی و رفع محدودیتهایی که خروجی کل را محدود میکنند، تمرکز کرده است. ازاینروی استفاده موفق از نظریه محدودیتها میتواند به افزایش ظرفیت تولید منجر شود.
- از آنسو تولید ناب روی حذف دورریز یا اتلاف از فرآیندهای تولید تمرکز میکند. در نتیجه اجرای موفق تولید ناب هزینههای تولید را کاهش خواهد داد.
هر دو روش تمرکز زیادی روی مشتری دارند و میتوانند شرکتهای تولیدکننده را سریعتر، قویتر و چابکتر کنند. بااینهمه تفاوتهای چشمگیری بین این دو وجود دارد. این تفاوتها را میتوان بدین شکل بیان کرد.
هدف
هدف نظریه محدودیتها، افزایش خروجی کل و هدف تولید ناب کاهش اتلاف و دورریز است.
تمرکز
در نظریه محدودیتها تنها تمرکز روی محدودیتهای موجود جهت حذف آنها است؛ اما در تولید ناب تمرکز زیادی روی حذف اتلاف از فرآیندهای تولید میشود.
نتیجه
نتیجهای که از نظریه محدودیتها حاصل میشود، افزایش ظرفیت تولید و نتیجه حاصل از تولید ناب کاهش هزینه تولید است.
موجودی
در نظریه محدودیتها موجودی را صرفا در حدی نگاه میداریم که خروجی را بیشینه کند. در تولید ناب تقریبا موجودی را حذف میکنیم.
تعادل خط
در نظریه محدودیتها عمدا تعادل خط را به نحوی به هم میزنیم که خروجی بیشینه شود؛ اما در تولید ناب برای حذف اتلاف در خط تولید تعادل ایجاد میکنیم.
سرعت
در نظریه محدودیتها سرعت تولید با بخش محدودیتدار توسط تکنیک طبل-حائل-طناب تعیین میشود؛ اما در تولید ناب، مشتری سرعت را تعیین میکند.
[imp content=”حذف منابع تنوع برای عملکرد بهینه یک خط تولید متعادل ضروری است.”]
از نگاه نظریه محدودیتها حفظ حدی از اضافه ظرفیت برای بخشهای بدون محدودیت، عملیتر و ارزانتر از حذف تنوع تولید یا تنوع تجهیزات برای تولید بیشتر است.
چنین کاری معادل ایجاد یک عدم تعادل عمدی در خط تولید است. حذف منابع تنوع برای عملکرد بهینه یک خط تولید متعادل ضروری است. بااینهمه حذف تنوع همچنان در نظریه محدودیتها مفید است؛ اما توجه بیشتر در این نظریه، افزایش بهرهوری است.
ترکیب نظریه محدودیتها با تولید ناب
یکی از قدرتمندترین جنبههای نظریه محدودیتها تمرکز بسیار بالای آن در رفع محدودیتها است. با اینکه در تولید ناب نیز تمرکز وجود دارد، اما معمولا از این تمرکز بهعنوان ابزاری برای کارهای مختلف استفاده میشود.
در دنیای واقعی همیشه باید چیزهای بیشتری را در نظر بگیریم؛ زیرا همه شرکتها منابع محدودی دارند. راستش همه جنبههای همه فرآیندها ارزش بهینهسازی ندارند و همه آنچه دور ریخته یا اتلاف میشود ارزش آن را ندارد که حذف شود.
از این نگاه نظریه محدودیتها میتواند بهعنوان مکانیسم بسیار موثری را برای اولویتبندی بهبود پروژهها عمل کند اما تولید ناب میتواند جعبهابزاری مملو از تکنیکهای گوناگون باشد. نتیجه اینکه کارایی تولید با حذف اتلاف از بخشهایی که محدودیت بیشتری دارند میتواند کارایی کل را به صورتی چشمگیر افزایش دهد.
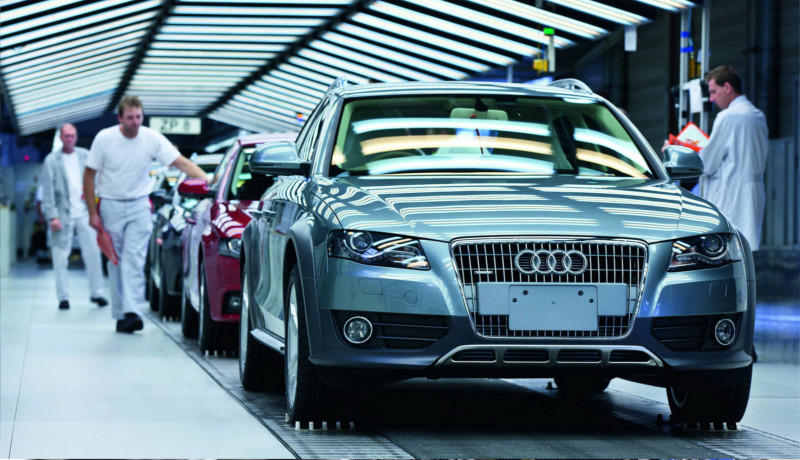
کارایی تولید با حذف اتلاف از بخشهایی که محدودیت بیشتری دارند میتواند کارایی کل را به صورتی چشمگیر افزایش دهد.
بااینکه ابزارها و تکنیکهای تولید ناب از ابتدا روی بخش محدودیتدار استفاده میشوند، میتوان آنها را روی تجهیزاتی که زیرمجموعه بخش محدودیتدار هستند نیز استفاده کرد؛ یعنی میتوان این تکنیکها و ابزارها را روی تجهیزاتی که باعث خالی ماندن یا قفل شدن بخش محدودیتدار یا در بخشهای بعدازآن که باعث از دست رفتن کیفیت میشوند، اعمال کرد.
ما در ادامه این مقاله میخواهیم توضیح دهیم که چگونه ابزارهای تولید ناب را میتوان در تکنیک پنج گام تمرکزی اعمال کرد.
استفاده از تولید ناب در گام «شناسایی محدودیت»
تولید ناب یک ابزار عالی به نام نقشهبرداری جریان ارزش (Value Stream Mapping) برای دنبال کردن جریان تولید دارد. در تولید ناب فلسفهای به نام گمبا (Gemba) وجود دارد که تاکید میکند که شما زمان بیشتری در واحد تولید سپری کنید. هرکدام از این دو، تاثیر یکتایی روی شناسایی محدودیتها دارد. در ادامه تاثیر هرکدام از این دو ابزار را در شناسایی محدودیتها آوردهایم.
نقشهبرداری جریان ارزش
- هنگام شناسایی محدودیت، مبنایی برای کار را ارائه میدهد؛ مثلا ممکن است چرخه زمانی هر مرحله روی این نقشه بهعنوان مشکل نمایش داده شود.
- تیمها را درگیر میکند و برای حل مشکلات مفید است.
- برای مستندسازی فرآیندها پیچیده، کارا است.
گمبا
گمبا ما را ترغیب میکند که زمان زیادی در واحد تولید بگذرانیم. قدم زدن در واحد، مشاهده تولید و حرف زدن با کارکنان میتواند روش بسیار موثری برای جمعآوری اطلاعاتی باشد که به کشف محدودیت کمک میکنند؛ زیرا مشاهده کردن فرآیند واقعی تولید و برهمکنش با کارکنان باعث میشود بتوانید درک عمیقی از فرایند واقعی تولید کسب کنید.
اعمال تولید ناب در گام «بهرهبرداری از محدودیت»
تولید ناب بهشدت روی استفاده از آنچه در دست دارید تاکید میکند. برای مثال تولید ناب اصول 5S را در طراحی محیط کار، ابزار کارخانه مجازی (Viasual Factory/Andon) را برای روحیه دادن به کارکنان، تکنیک کار استانداردشده (Standardized Work) را برای بهکارگیری بهترین روشها و تکنیک کایزن (Kaizen) را برای طوفان ذهنی ایدهها جهت بهبود کار پیشنهاد میکند.
اصول 5S
- مبنایی برای عملکرد بهتر در محدودیت ارائه میدهد.
- امکان تشخیص سریع مشکلات جدید در بخش محدودیتدار را فراهم میکند.
- با بهبود محیط کار باعث افزایش انگیزه و روحیه کارکنان میشود.
5S برنامهای است که باعث حذف اتلافهایی میشود که از طراحی ضعیف محیط کاری حاصل میشوند. 5S روی پنج عنصر تأکید دارد:
- ساماندهی: حذف آنچه لازم نیست.
- نظم و ترتیب: مرتب و منظم کردن اشیای موجود.
- پاکیزگی: تمیزکاری و بررسی محیط
- استانداردسازی: ایجاد استاندارد برای 5S
- انضباط: اعمال دائمی استانداردها
کارخانه مجازی
- معیارهای تولید بخش محدودیتدار را در زمان واقعی نمایش میدهد.
- با هشدار لحظهای به اپراتور برای دخالت در کار دستگاه، زمان واکنش را کاهش میدهد.
- امکان ارائه هشدار برای توجه سریع به بخش محدودیتدار را فراهم میکند.
- تمرکز را با استفاده از ابزارهای افزایش تمرکز بصری در مورد اجزای مهم بخش محدودیتدار افزایش میدهد.
کارخانه مجازی یک استراتژی برای نمایش بصری اطلاعات جمع شده از واحد تولیدی را فراهم میکند. Andons نمایشگرهای بصر هستند که وضعیت تولید را نشان داده و هنگامیکه مشکلی پیش بیاید سریع اپراتور را متوجه میکنند تا مشکل را هر چه سریعتر رفع کنند.
کار استانداردشده
- کار استانداردشده بهرهوری را با اجرای دائمی بهترین تمهیدات بهبود میدهد.
- میزان تنوع را با اعمال پروسههای استاندارد در بخش محدودیتدار کاهش میدهد.
- باعث میشود همه اپراتورها بخش محدودیتدار را به روشی قابل تکرار نصب و اجرایی کنند.
کار استانداردشده بهترین روشی را که دائما توسط اپراتورها اجرا و بهروزرسانی میشود، ثبت، نگهداری و بهبود میدهد.
کایزن
- کایزن (Kaizen) یک مکانیسم خوب برای تولید ایدهها و بهرهبرداری از آنها روی بخش محدودیتدار است.
- کایزن روشهای سریعی را که به افزایش بهرهوری بخش محدودیتدار ختم میشوند، شناسایی میکند.
- کایزن اپراتورها را درگیر عملکرد تیمی و تفکر تیمی در مورد کار میکند.
این تکنیک چهارچوبی برای فعالیت کارکنان در گروههای کوچک میسازد و بهبودهای دائمی را در فرآیند تولید اجرایی میکند. کایزن استعدادهای شرکت را دور هم جمع میکند تا بهبود دائمی را تضمین کنند.
اعمال تولید ناب روی «زیرمجموعههای بخش محدودیتدار»
تکنیک کانبان (Kanban) برای منظم سازی جریان تولید و تکنیک کنترل خط (Line Control) برای هماهنگسازی خطوط تولید، میتوانند جهت هماهنگ کردن بخشهای گوناگون با بخش محدودیتدار استفاده شوند.
کانبان
- کانبان یک ابزار بصری برای کنترل جریان مواد در خط تولید فراهم میکند.
- مصرف مواد در بخش محدودیتدار را با مواد بخشهای پیشین با استفاده از کنترل تزریق مواد جدید به فرایند، هماهنگ میکند.
- کانبان روشی برای منظم سازی جریان مواد است.
کنترل خط
- کنترل خط یک روش مؤثر و خوب برای جایگزینی با تکنیک طبل-حائل-طناب برای خطوط تولید کالاهای پرمصرف (Fats Moving Consumer Goods or FMCG) است.
- این ابزار سرعت کار بخشهای محدودیتدار و بدون محدودیت را برای بیشینهسازی خروجی و کاهش توقفها، بهینه میکند.
- کنترل خط با هماهنگسازی تجهیزات هنگام روشن شدن، مدتزمان روشن شدن بخش محدودیتدار را کاهش میدهد.
کنترل خط یک تکنیک پیچیده است که برای خطهای تولید هماهنگ مثل خطوط تولید کالاهای پرمصرف به کار میرود. این تکنیک بخشهای غیرمحدودیتدار را عملا در کنترل بخش محدودیتدار قرار میدهد و از این طریق خروجی کل سیستم را افزایش میدهد.
اعمال تولید ناب در گام «افزایش عملکرد بخش محدودیتدار»
تولید ناب تکنیکهای برای نگهداری پیشگیرانه از تجهیزات (TPM)، کاهش بسیار زیاد زمان تغییرات (SMED)، ایجاد ابزارهای تشخیص و جلوگیری از نواقص در فرآیند تولید (Poka-Yoka) و اتوماسیون بخشی از تجهیزات (Jidoka) دارد.
همه این تکنیکها هنگام افزایش عملکرد بخش محدودیتدار کاربرد مستقیمی دارند. TPM و SMED را میتوان یک روش بهرهبرداری نیز نامید زیرا با این دو ابزار میتوان خروجی را با منابع موجود بیشینه کرد. این ابزارها تا حدودی پیچیده هستند و احتمالا بهتر است برای اجرای آنها از متخصصین خارج از مجموعه کمک بگیرید.
TPM
- این ابزار خرابیها و توقفهای بخش محدودیتدار را کاهش میدهد.
- حس قدرتمندی از کنترل داشتن روی تجهیزات به اپراتور میدهد.
- امکان اجرای عملیات نگهداری را در خارج ساعت کاری فراهم میکند.
- این ابزار با یافتن و از بین بردن دلایل ریشهای نواقص، کیفیت را افزایش میدهد.
TPM یا Total Productive Maintenance یک رهیافت همبسته برای نگهداری دارد. این رهیافت روی پیشگیری از نواقص تمرکز میکند و مدتزمان عملیاتی بخش محدودیتدار را با افزایش مدتزمان کار، کاهش چرخههای زمانی و حذف نواقص بیشینه میکند.
SMED
- این تکنیک مدتزمان مفید تولید را در بخش محدودیتدار افزایش میدهد.
- اندازه بستههای تولیدی را کاهش میدهد و باعث میشود قدرت پاسخگویی به تقاضای مشتریان افزایش یابد.
- شروع کار را یکنواختتر میکند؛ زیرا در یک فرآیند تغییرات ساده و استانداردشده، کیفیت و کار مداوم سیستم را بهبود میبخشد.
SMED یا Single-Minute Exchange of Dies روشی برای کاهش بسیار زیاد مدتزمان تغییرات بخش محدودیتدار است.
Poka-Yoka
- این ابزار تعداد نواقص را کاهش میدهد. این کاهش نواقص نهفقط در بخش محدودیتدار، بلکه در بخشهای دیگر هم مهم است.
- این امکان را به اپراتور میدهد که زمان بیشتری روی نگهداری خودکار صرف کند.
تکنیک Poka-Yoka تجهیزاتی برای تشخیص و پیشگیری از نواقص در داخل خود دستگاهها طراحی و ایجاد میکند. هدف از این کار صفر کردن نواقص است.
Jidoka
- در برخی از موارد نمیتوان محدودیت را بدون سرمایهگذاری بزرگ رفع کرد. Jidoka میتواند راهنماییهای ارزشمند برای طراحی و ارتقا تجهیزات ارائه دهد.
Jidoka به معنای اتومایسون هوشمند یا اتوماسیون با حس انسانی است. نتیجه استفاده از این تکنیک این است که ما بدانیم خودکارسازی بخشی از فرآیند، به طرز چشمگیری ارزانتر ازخودکارسازی کل سیستم است. Jidoka همچنین ابزارهای برای توقف خودکار هنگام بروز نواقص دارد.
آخرین مقاله درباره نظریه محدودیتها
مقاله حاضر آخرین مقاله از سری مقالات در معرفی نظریه محدودیتها است. ما در این سری از مقالات تلاش کردیم تصویری ساده و روشن از چیستی و چگونگی عملکرد این نظریه عرضه کنیم.
اگر فکر میکنید نظریه محدودیتها میتواند روی میزان خروجی واحد تولیدی شما هم اثر بگذارد، شاید این سری از مقاله بتوانند کمکتان کند.